Critical Path Joinery
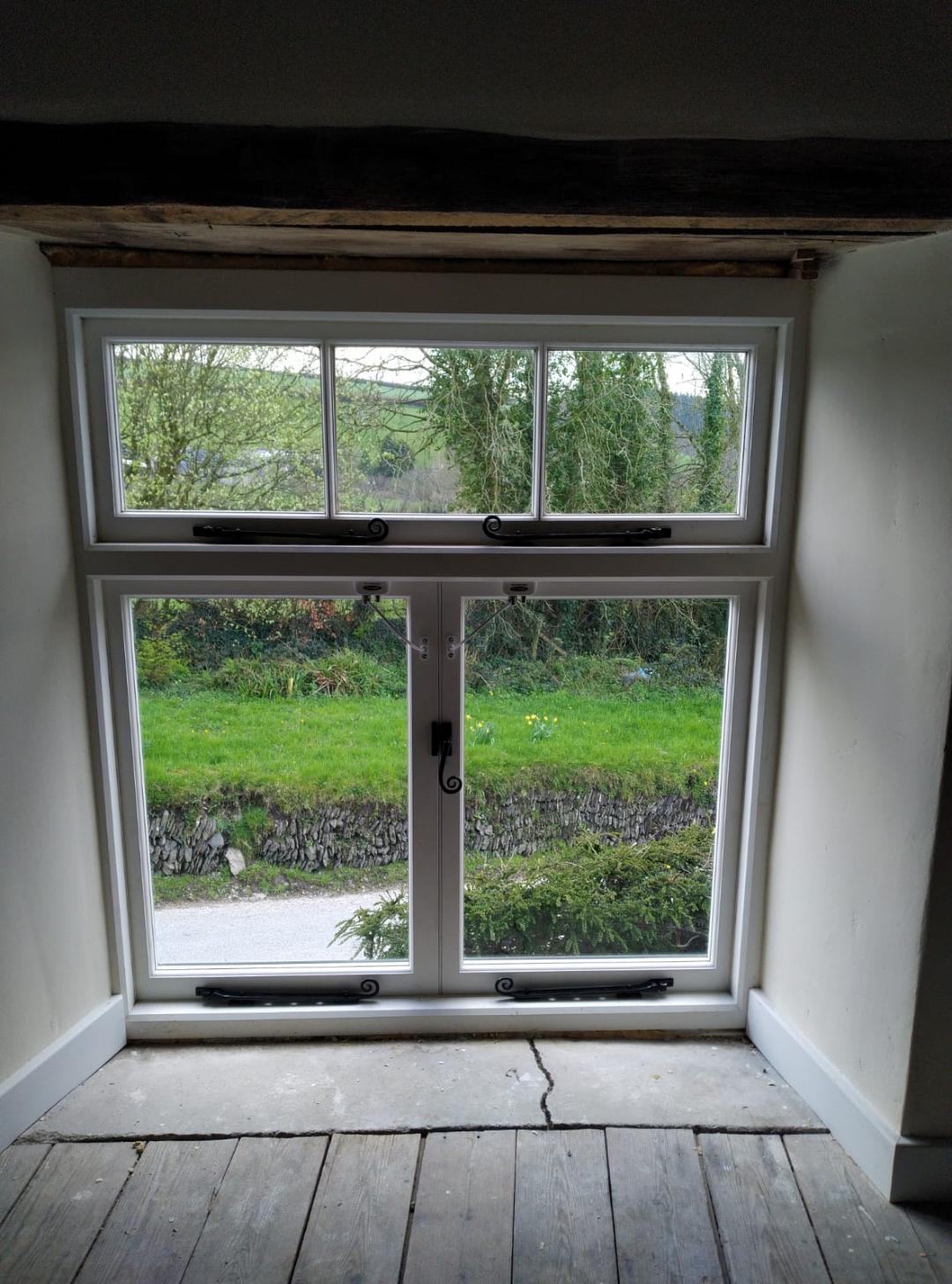
I didn't know how to define this, but "Critical Path Joinery" seemed as accurate as I could get. What do I mean by that? I mean something that must happen by a set date.
Examples of this might be work in a holiday let and you have guests coming. You need joinery because other trades are booked and are due to follow the installation of the joinery.
Firstly, it's essential that you book your joinery well in advance. Unlike general building materials you collect from a builder's merchant, everything we make has to be made from scratch. There's not an inventory of joinery waiting for you.
You need to think ahead and have the joinery made and ready to be collected. Ideally we would have the joinery here and waiting for at least two weeks in advance of your deadline.
Here's some tactics that may help you to smooth your journey as much as possible.
If your project is a new build agree the sizes of the windows and doors with us and the contractor. The contractor can then ensure the opening are made to the correct sizes. For some strange reason this is often not an approach that it is used. It's as if clients and contractors are afraid to make the openings. Please do understand that if you build everything and then ask for a survey you have just created an unnecessary delay.
Know what's going on! I've arrived to jobs many times and wanted to measure. I've asked questions such as "Where is the finish floor level?" and "Where are you putting the lintels in?" only to be confronted with a shrug of the shoulders. Again, there's no reason why something can't be made in advance and the opening made to suit.
Sign your Purchase Order and Pay your Deposit Invoice. Without us being in receipt of these we will not start your project and we will not hold our production schedule for you. We offer our service on a first come, first served basis.
Reduce variation! We've had some really interesting joinery come through recently. Stained finished inside, exterior frame one colour, exterior casement another. This creates so much more work. We're happy to provide the service and it looks great! Luckily the job is not time sensitive and a quality outcome was all the client wanted. But if things were all one colour it would be much faster!
It is now only after 25 years after joining our nearly 100 year old fmaily business I see how many of these issues play out. It is why I try I provide these guides so you have the information you need and you are clear on what's needed to avoid dissapointment. It also gives me the confidence to look at a situation and say if a project is realistic or not based on the circumstances.